Cans are becoming increasingly popular because they ensure good protection from mechanical impact, and are water, gas and microorganism resistant.
Packaging structure
Metal packaging has been preserving and protecting food for more than 200 years but the materials and coatings have changed; today, the food industry uses steel tinplate and aluminium. The first can was developed in 1810 for transport convenience and food shelf-life extension. Cans are still used today.
Delamaris is heavily invested in new aluminium fish packing technology to make its products easier to open, lighter to transport and highly recyclable. Aluminium is the third most common material in nature, just after oxygen and silicon; it is very convenient for packaging because it’s corrosion and sound resistant, and our cans are coated with a thin layer of it to prevent substance transfer between packaging and content and provide external impact protection.
Aluminium is 100% recyclable
Each tonne of recycled aluminium prevents 9.5 tonnes of CO2 environmental nuisance because of the low amount of energy used in its production. The production of 100% recycled aluminium consumes 95% less energy than the production of aluminium from new raw materials. The percentage for steel production is only 75%.
Less packaging, more care for the environment
When changing from tinplate to aluminium packaging, Delamaris also renovated its design, which eliminated secondary packaging for the majority of its products, thereby delivering additional energy savings and further protecting the environment.
Read more
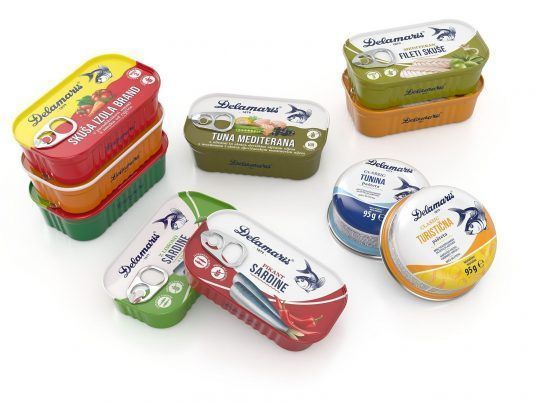
So many flavours! Which one to choose?
We have a wide range of different flavours for you. There’s something for everyone. You can choose tuna or mackerel, with or without added vegetables and tomato sauce. Are you ...
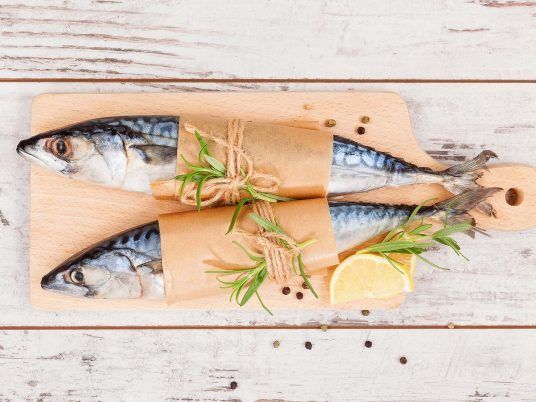
What kinds of fish swim in Delamaris’ cans?
Mackerel (Lat. Scomber spp.), used for products that combine fish and vegetables, in fillet form or in our Tourist pâté, is a blue fish caught all over the world. It ...
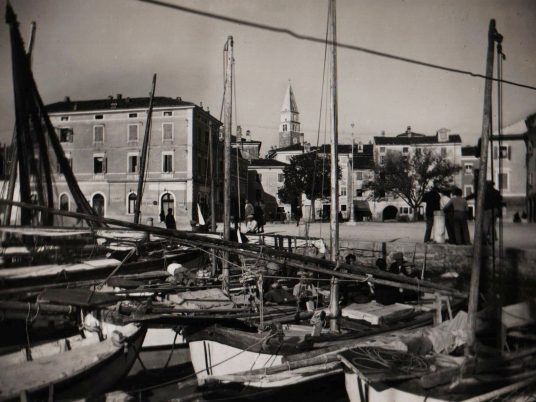
We’re proud of our fish can’s rich history
Slovenian trademarks are the product of the diligent hands of many generations proudly creating the future. Delamaris is a collection of stories and flavours, and our knowledge and tradition of ...